Causes and prevention of quenching cracks on smls pipes
The main production process of smls pipe is as follows: refining → continuous casting of tube billet → heating of tube billet → perforation → hot rolling → diameter determination (reduction) → heat treatment. In the process of heat treatment, quenching cracks sometimes appear. Quench crack is a kind of crack defect perpendicular to the steel pipe surface, whose crack tip is sharp and the degree of decarbonization is light, which is caused by the structural stress and thermal stress generated by rapid cooling exceeding the strength of the pipe. According to the different microstructure of quenching crack, the causes are varied.
1. Type and cause of quenching crack
1.1 Surface defect induced quenching crack
When φ114.30mm x8.56mm 26CR-MO4s alloy structure tube was rolled by a unit, small quenching cracks often appeared in the inner wall, as shown in Figure 1 and Figure 2. The microscopic morphology photos of the polished state show that there are many surface defects, such as pits and warping, whose depth is not more than 0.2mm, in the inner wall of the tube. These defects produce stress concentration under the action of quenching stress, which is the reason for inducing quenching cracks.
FIG 1
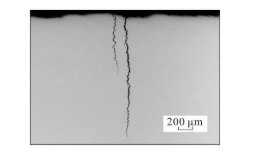
FIG 2
Surface defect-induced quenching cracks mostly appear in small diameter, thin - walled steel tubes. On the one hand, the rolling elongation of small-diameter steel pipe is larger, and the original defects such as pits and streaking are easy to appear on the inner and outer surfaces of the pipe. At the same time, during the quenching and cooling process, the stress concentration effect of the surface tension stress on the defect position is more significant, so the defect-induced quenching crack is easy to appear.
In addition, when rolling φ88.90mm x 6.45mm 20 steel tubing, quenching cracks induced by surface defects were also found on the inner and outer surfaces.
1.2 Stress cracking quenching crack
Stress cracking is a common type of quenching crack, which is caused by surface tensile stress exceeding material strength during quenching and cooling.
The surface quenching crack morphology and surrounding microstructure of φ177.80mm x 11.51mm N80Q steel casing are shown in FIG. 3 and 4. As can be seen from Figure 3 and 4, the surface of the pipe body with stress cracking quenching crack is smooth and smooth, without original defects, and the microstructure is uniform and small. The crack is caused by excessive surface tensile stress. The stress cracking quenching crack is completely perpendicular to the surface of the tube body and extends along the wall thickness direction, which also indicates that this kind of crack is completely caused by excessive surface tensile stress.
FIG 3
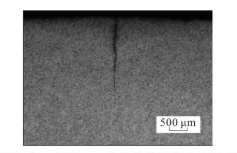
FIG 4
In addition, stress cracking quenching cracks also appear when φ139.70mm x 10.54mm P110 steel bushing is rolled. The excessive stress on the surface of the tube is mainly caused by the uneven cooling of the inner and outer walls of the tube. Improper cooling will lead to large residual tensile stress on the surface of the tube body and increase the risk of stress-type quenching cracking.
1.3 Surface carburized quenching crack
When medium carbon CR-Mo microalloy steel with C content of about 0.30% is used to produce seamless steel tubes, quenching cracks often appear on the surface of the tubes. The reason for the formation of the quenching crack is that there is local carburization phenomenon on the external surface of the tube, which leads to excessive stress in the carburized part during the quenching process, and thus the quenching crack is formed.
According to the production process of seamless steel tube, it is speculated that 101 processes may lead to the increase of C content on the surface of steel tube:① the tube return surface is bonded with high-carbon protective slag, which penetrates into the matrix during the high temperature heating process of annular furnace, resulting in local carburization on the surface of capillary tube after rolling; ② The surface of the steel pipe before entering the heat treatment furnace is sticky with oil, wood chips and other high-carbon foreign substances, which leads to the surface C content higher than the matrix after high-temperature heat treatment.
1.4 Quenching crack of crack sensitive section steel
Due to the high content of alloying elements and the high strength of the tube body, some high grade seamless steel tubes have a high stress field strength factor and belong to the crack sensitive type steel. The surface or internal microscopic defects of the pipe are very easy to expand under the action of stress, thus forming cracks.
Grade S135 steel alloy structure pipe surface quenching crack defects probability significantly higher than that of other steel grade, since the steel containing Cr, Mo alloy elements more, tubing, high strength steel tubes microstructure coordination plastic deformation ability is poorer, the release of deformation store can only through to form a new way of surface crack, therefore belongs to high risk of quenching crack pipes.
2. Preventive Measures
Quenching crack is a kind of defect caused by stress cracking, which is generated when the internal stress of the material exceeds the fracture strength. The causes are very complex. The internal stress is formed in the quenching process and has the property of tensile stress. The internal cause of quenching crack is the excessive stress during martensitic transformation of the material during quenching, which is closely related to the chemical composition of the steel, mainly the content of C and alloying elements. Generally, the higher the content of C, the easier it is to produce cracks. At the same time, quenching cooling mode, steel pipe surface quality and other external factors may also lead to quenching cracks.
According to various factors that may lead to quenching cracks, the following preventive measures can be taken.
(1) Preventive measures for surface defect induced quenching crack. For quenching cracks caused by local stress concentration induced by surface defects, it is necessary to improve the surface quality of the rolled tube body and reduce macroscopic defects and shape mutation of the material.
(2) Preventive measures for stress cracking type quenching crack. Reducing the cooling rate can reduce the residual stress to a certain extent, that is, reduce the structural stress caused by the transformation of maltensite, and the transformation process of inner and outer wall is in a gradient. On the premise of ensuring the cooling rate of all martensite structures (50-609C /s), the cooling water flow rate is appropriately reduced, and the cooling method of internal spraying + external spraying (delayed) is adopted. Theoretically, the delay time of external spraying cooling relative to internal spraying cooling is the time required from the beginning to the completion of martensite transformation in the inner wall of steel pipe, which causes the compressive stress to be generated around the pipe body. When the residual compressive stress is generated in the circumferential direction of the tube, the quenching crack can be greatly reduced or completely eliminated.
(3) Preventive measures for surface carburizing quenching crack. ①Appropriately increase the viscosity of the slag, reduce the slag consumption, the liquid slag layer will thicken, prevent the fluctuation of the liquid steel surface; At the same time, with the increase of slag viscosity, the diffusion rate of carbon in slag layer to molten steel will slow down greatly. ② Adding an appropriate amount of oxidant (such as MnO2) to the slag can promote the oxidation of carbon in the slag, and effectively inhibit the carbon content in the enriched carbon layer and slag layer; Or use carbon-free slag.
(4) Preventive measures for quenching crack of crack sensitive section steel. Adjust the steel composition properly, reduce the content of C element, refine the grain, and improve the crack propagation resistance. The mass fraction of C and Mn should be strictly controlled for the water-quenched steel. When W (C)+ Ru (Mn)/3≥0.9%, the water quenching process has the risk of cracking, and the oil quenching process is recommended. For high C and high Mn steel, reducing the quenching temperature and cooling speed is beneficial to prevent the formation of quenching cracks.
3. conclusion
(1) The pipe surface defects caused by rolling process tend to produce stress concentration after quenching, which is the reason for inducing quenching cracks; Therefore, the rolling process parameters are optimized to improve the surface quality of pipes and reduce the macroscopic defects and shape mutation of materials.
(2) Unreasonable quenching cooling method will lead to large residual tensile stress in the pipe body, which will increase the risk of quenching crack. it is an effective measure to reduce residual stress and eliminate quenching crack by adjusting the sequence of inner and outer spray and water flow of cooling water of pipe body.
(3) The molten steel level in the mold is unstable, and the carburization of the casting billet caused by the contact between the carbon-rich layer formed by the protective slag and the molten steel is one of the reasons for the carburization of the casting billet. Can be through the use of heating type. Slag or non-carbon protection slag, as well as the control of the injection flow, casting speed, mold vibration frequency and other process factors are stable, prevent the fluctuation of the liquid steel surface, maintain a stable liquid slag layer thickness.
(4) Properly adjust the steel composition of crack sensitive pipe, and rationally select the cooling medium and cooling speed according to the mass fraction of C and Mn.