1. Internal surface defects of seamless steel pipes:
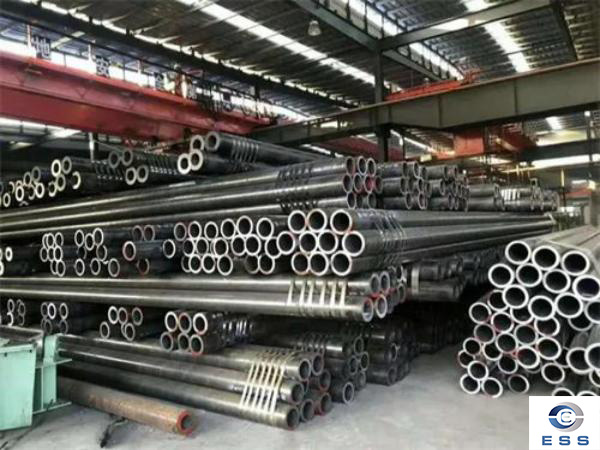
- Inward folding characteristics: linear or spiral sawtooth defects, caused by tube blank quality, uneven heating, improper adjustment of punching machine parameters, etc.
- Internal scarring: Scarring appears, caused by impurities in graphite lubricant, iron ears in unused pipes, etc.
- Warped skin: small raised skin in the shape of nails. Causes include improper adjustment of punching machine parameters, sticking of steel on the head, accumulation of iron oxide scale, etc.
- Inner straight track: There are linear scratches with a certain width and depth. The causes include metal hard objects stuck to the mandrel, impurities in the graphite, etc.
- Inner edge: There is a linear protrusion with a certain width and depth. The reasons include serious wear of the mandrel and uneven grinding.
- Inner bulge: regular bulging, caused by excessive grinding of continuous rolls, etc.
- Dimples: regular or irregular pits, caused by improper adjustment of continuous rolling and uneven heating of the tube blank.
- Internal threads: There are spiral marks on the inner surface of the steel pipe, which mostly appear on the inner surface of thin-walled pipes. The causes include inherent defects in the cross-rolling process and excessive wall reduction.
2.
Exterior surface defects of seamless steel pipes:
The first type is external folding, which is characterized by spiral layered folds on the outer surface of the steel pipe. The cause may be that there are folds or cracks on the surface of the tube blank, or the subcutaneous pores or subcutaneous inclusions of the tube blank are serious, or the surface of the tube blank is cleaned. Bad etc.
The second type is separation layer, which is characterized by spiral or massive delamination and cracking on the surface of the steel pipe. The cause may be serious non-metallic inclusions, residual shrinkage cavities or severe looseness in the tube blank.
The third type is scarring, which is characterized by scars on the outer surface of the steel pipe. The cause may be that the roller sticks to steel, is aged, has serious wear, or has foreign matter stuck to the conveyor roller or is seriously worn.
The fourth type is pitted surface, which is characterized by uneven pits on the surface of the steel pipe. The cause may be that the steel pipe stays in the furnace for too long or the heating time is too high, or the high-pressure water phosphorus removal equipment does not work properly.
The fifth type is the green line, which is characterized by symmetrical or asymmetric linear rolling marks on the outer surface of the steel pipe. The cause may be misalignment or severe wear of the sizing machine, or poor roll processing.
The sixth type is hair lines, which are characterized by continuous or discontinuous hair-like fine lines on the outer surface of the steel pipe. The cause may be that the pipe blank has subcutaneous pores or inclusions, or the surface of the pipe blank is not thoroughly cleaned.
The seventh type is reticular cracks, which are characterized by small fish-scale cracks with strips and large pitch on the outer surface of the steel pipe. The cause may be excessive content of harmful elements in the tube blank, or aging of the perforation roller and steel sticking, etc.
In addition, scratches, dents, bruises, dents, rolling and cracking on the surface of steel pipes are all common defects in the steel pipe manufacturing process. Scratches are mainly caused by mechanical action and transportation. When grinding, ensure that the outer diameter and wall thickness are not lower than the standard requirements. Collapsing is caused by lifting, straightening, etc. It can exist locally and the surface is smooth. If it is out of tolerance, it needs to be removed. Bruises are caused by various collisions. They can exist when the local depth does not exceed 0.4mm. If they are out of tolerance, they need to be smoothed and polished.
Straightening dents are caused by improper operation or wear of the straightening machine. Straightening dents without obvious edges and corners are allowed and the outer diameter meets the tolerance requirements. If it exceeds the standard, it needs to be removed. Rolling folds are caused by improper pass selection, improper adjustment of the rolling mill, or improper distribution of the reduction of each stand of the continuous rolling mill, etc., and are not allowed to exist. Cracks mostly occur on thin-walled tubes and are caused by uneven heating temperatures of the tube blanks, improper adjustment of the continuous rolling mill speed and roll gap, the influence of the capillary wall thickness, and inclusions in the tube blank itself, and are not allowed to exist.
3.
Judgment:
- Casing and general pipes are allowed to have inner straights with a depth not exceeding 5%, and inner straights with sharp edges should be smoothed.
- Casings and line pipes are allowed to have inner edges with a height not exceeding 8% of the wall thickness. If the height exceeds 8% of the wall thickness, they should be ground and re-cut.
- For steel pipes required for L2 level flaw detection, the inner edge height shall not exceed 5%. Sharp inner edges should be smoothed.
- The negative deviation of the wall thickness is not exceeded, and the concavity where the actual wall thickness is greater than the required minimum value of the wall thickness is allowed to exist. Exceeding dents should be removed.
- The depth of defects in the internal thread of the steel pipe is not greater than 0.3mm and is within a certain tolerance range.
Read more: Din en 10220 seamless steel pipes